|
|
|
STEP 1 of 10 - Configuration |
 |
|
Previous |
Next |
|
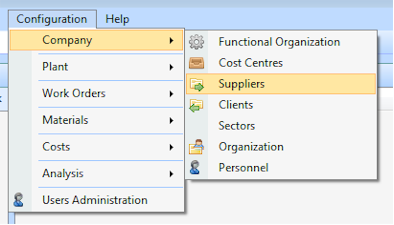 System configuration is the first step in any maintenance management software.
This first step is very important, as you will set basic
rules that will follow the organisation for many years, so you should make wise
decisions.
InnWinWin is already pre-configured for a typical building and ready to use,
although some adjustments to your specific case are required.
In this wizard, we will focus on the system’s main configurations.
 |
ECompany - Functional organisation |
|
Functional organisation is like an X-ray of your
plant where you see all the systems inside it and the
equipments that contribute to the performance of each
function – forklifts, cranes & suspensions, electrical
workshop, etc... Coordinating your equipments into
systems enables you to analyze them individually and
diagnose problems that may affect the overall
performance of a specific system. Functional
organisation gives you a detailed description of your
plant in an engineering point of view. |
|
|
 |
Company - Cost Centers |
|
Maintenance information is expressed in a financial
point of view through Cost Centers. A concise and
convenient way for Financial Departments to analyze
maintenance. You may typically consider each plant a
cost center, within which you will have sub-cost
centers. |
|
|
 |
Company - Suppliers |
|
Suppliers that are relevant for maintenance:
maintenance service providers, equipment manufacturers
or resellers and parts and materials suppliers. |
|
|
 |
Company - Clients |
|
Setting up and recording clients only makes sense for
maintenance service providers that wish to manage their clients plant
maintenance with ManWinWin 5. |
|
|
 |
Company - Technical Intervention Area |
|
Organizes the internal structure of the people actually carrying out maintenance
operations in the form of an organisational chart, where the several functions
are specified in a hierarchy and where the people performing the maintenance can
be coordinated.A maintenance department, even with more than one workshop, is typically
organized into intervention areas like Electrician, Polyvalent, Plumber,
Foreman, among others. A standard man-hour cost is established for
each intervention area and this cost must reflect
average cost with assigning a specific technician to
maintenance work. |
|
|
 |
Company - Personnel |
|
All people – internal or external personnel – with
possible intervention in maintenance tasks must be
recorded into the software and assigned a specific
technical intervention area (as seen above). |
|
|
 |
Plant - Item types |
|
Setting up your plant’s Item Types means creating a consistent coding system for
your maintenance items. With a simple and suggestive two-letter system, you may
establish, for example, PU = PUMP, PP = Piping, etc…
Each Item Type has a technical datasheet which you can
customize. You have up to 40 particulars with which you
can characterize the item and then use for search
filters or cross analysis. |
|
|
 |
Plant - items families |
|
Item family may be an interesting feature for you.
In practice, this feature allows you to group
maintenance items according to its basic function,
enabling you to analyze these particular groups
individually |
|
|
 |
Work Orders - Causes & Symptoms |
|
A set of key descriptions used to characterize
breakdowns. This feature enables all users in the
organisation to use a uniform language when addressing
breakdowns and allows important cause and symptom
analysis. |
|
|
 |
Work Types |
|
When managing maintenance, it is useful to set different Work Types. This
classification allows the manager to sort out Effort and Costs of each
maintenance type, giving him very good insights on which maintenance types are
Effort and Costs mostly concentrated, providing valuable information for results
optimization. Maintenance Work can be classified into 3 major types that can still be divided
into “sub-types”:
- Systematic Maintenance
(Preventive Systematic, inspections, lubrications)
- Condition based (preventive based on
equipment condition)
- Corrective Maintenance (Repairs) |
|
|
 |
Materials – Stock item coding standard
|
|
Stock item coding standard – this means establishing a structured organisation
of Classes, Families and Sub-Families. The idea is to create a logical structure
Class / Family / Sub-Family through
which the manager will organize and have, inside each structure, only a
reasonable amount of different stock items, easily searchable.
Example: Class C – Consumables, Family AV –
HVAC, Sub-Family FI – Filters, 023 – Sequential number. |
|
|
 |
Costs – Accounts |
|
Account means organising a cost by its nature or its
type. The manager should set relevant Accounts that fall
into his area of responsibility. |
|
|
 |
Costs – Document Types |
|
Document types are a mandatory configuration to
create cost documents and cost items. Invoice, Receipts,
delivery notes are typical cost documents. |
|
|
Tips & best practices |
 |
Configuration of the system must be seen
as the foundations of a building. This
stage requires some time and thought. |
 |
Tree structures (Ex: Cost centers, staff
organisation, etc…) should not have too
many levels. Keep it simple and friendly
for all users in your organisation. |
 |
Before defining any coding system,
always bear in mind an upper limit and,
according to that upper limit, start
your codes with zeros on the left.
Example: if you have up to 1000
suppliers, start with Supplier nr. 0001,
nr. 0002, … , nr. 0345, and so on. |
|
|
|
|
|
|
|
|
|
Products |
|
|
Contact us |
|
|
|
|
|